Since 2019 Concentrator advanced from Wemco flotation cells to tank flotation cells. The final milled product at 80% passing 0.15 mm is fed to the Tankcells Flotation Plant (TFP) with capacity of 1 745 t/hr, which is a counter-current circuit, where the copper is concentrated into the overflow of the rougher, cleaner and re-cleaner flotation stages. The underflow from re-cleaner and cleaner stages is recycled to the rougher cells for further copper extraction. Chemical reagents such as collector and frother are used during the flotation process. The final concentrate from the re-cleaner overflow is pumped to the Copper Filter Plant (CFP) for dewatering and drying, whereas the final tailings from rougher cells are pumped to the magnetic separation plant (stream 1) for magnetite recovery.
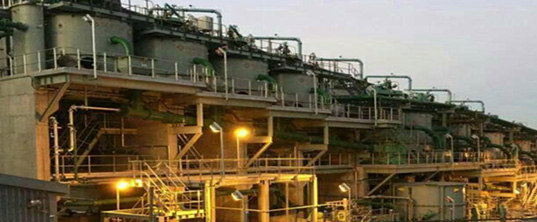